
ÍNDICE
1-¿Qué es un material sintético?
2-¿Qué es sintetizar materiales?
3-¿A qué nos referimos cuando hablamos industrialmente de materiales sintéticos?
4-Hitos históricos que marcan la vida de los materiales sintéticos.
5-Materias primas para la producción de materiales sintéticos.
1-¿Qué es un material sintético?
Antes de dar a conocer lo que es un material sintético, daré a conocer un poco de la historia sobre este tema. Los materiales sintéticos no se encuentran en la naturaleza, sino que los seres humanos son aquellos que los fabrican,es decir, son materiales artificiales. El inicio de todo este mundo material comenzó en el año 1860 con la aparición del celuloide. Este material se creo a partir de la modificación química de las moléculas de celulosa que se encuentran en las plantas. Una gran contra de este material era su inflamabilidad y sensibilidad a la luz. En 1862, Alexander Parkes creó un material duro que podía ser moldeado (parkesina), primer material semi-sintético. En 1906 Leo Hendrik Baekeland creó la Baquelita, un material sintético que al contrario de todos los plásticos en vez de derretirse, se endurecía.

Alexander Parkes
Después de la primera guerra mundial, se comenzó a crear materiales sintéticos derivados del petróleo. El polimetilo de metacrilato o mas llamado " plexiglas", fue uno de los materiales más famosos de la época.
Definición de material sintético:
Son elementos químicos creados artificialmente y cuya existencia no ha sido observada en la naturaleza. Son elementos radiactivos, es decir inestables, con vidas medias cortas en comparación con la edad del planeta. Por lo tanto se desintegraron casi totalmente desde la formación de la Tierra, y no se encuentran en cantidades apreciables salvo por la acción humana, producidos en reactores nucleares o aceleradores de partículas.
2-¿Qué es sintetizar materiales?
La sintetización es el proceso industrial por el cual se consigue crear piezas que son complicadas de obtener por otros procedimientos como el forjado o el mecanizado. Consiste en reducir el material base a polvo para luego comprimirlo en un molde a una determinada presión y calentarlo a una temperatura controlada.
Sintetizar un material:
Una de las propiedades de los elastómeros es la elasticidad, tienen la posibilidad de experimentar grandes deformaciones y de recuperar elásticamente su forma primitiva. Probablemente este comportamiento se observó por primera vez en los cauchos naturales, sin embargo, en los últimos años se sintetizan gran número de elastómeros con gran variedad de propiedades.
En ausencia de esfuerzos. los elastómeros son amorfos y están compuestos de cadenas moleculares muy torsionadas, dobladas y plegadas. La deformación elástica causada por la aplicación de un esfuerzo de tracción origina un enderezamiento, desplegado y alargamiento de las cadenas en la dirección del esfuerzo de tracción. Tras eliminar el esfuerzo, las cadenas recuperan la configuración original y las piezas macroscópicas vuelven a tener la forma primitiva.
La fuerza impulsora de la deformación elástica es un parámetro termodinámico llamado entropía, que mide el grado de desorden del sistema. La entropía crece al aumentar el desorden, al aplicar un esfuerzo a un elastómero. las cadenas se alargan y se alinean, es decir, el sistema se ordena. A partir de este estado, la entropía aumenta al volver las cadenas a su original estado, este efecto entrópico origina dos fenómenos: en primer lugar al aplicar un esfuerzo al elastómero, este aumenta su temperatura y en segundo lugar, el módulo de la elasticidad aumenta al incrementar la temperatura, este es un comportamiento contrario al de otros materiales.
3-¿A qué nos referimos cuando hablamos industrialmente de materiales sintéticos?
Clasificación de los materiales sintéticos: en función de su estructura interna se clasifican en:
Termoplásticos: Están formados por macromoléculas lineales o ramificadas, no entrelazadas. En general son duros en frió y al calentarlos se reblandecen y fluyen.
El proceso de calentamiento y enfriamiento para darles forma para que endurezcan con la forma deseada, puede repetirse prácticamente de forma ilimitada. Algunos ejemplos de este tipo son: polietileno , el cloruro de polivinilo , poliesterol, polipropileno.....Se usan para el aislamiento de cables eléctricos, calandras,interior del motor, salpicaderos....
Termoestables: Se denominan así por no sufrir ninguna variación en su estructura al ser calentados, ni se reblandece al ser sometidos a grandes temperaturas, siempre y cuando no se llegue a la temperatura de descomposición. Entre los materiales termoestables se encuentran las resinas fenólicas, resinas alquídicas, resinas de poliester no saturadas.... Se usan para fabricar portones, capos, salpicaderos.
Elastómeros: Son materiales macromoleculares, que en un amplio margen de temperaturas, pueden sufrir, sin rotura, deformaciones considerables (estiramientos) bajo la acción de fuerzas relativamente pequeñas y recuperar posteriormente su longitud primitiva. Podemos encontrar cauchos naturales y sintéticos , poliuretano.. Se utilizan en revestimientos interiores, asientos.
Elementos sintéticos utilizados en el vehículo:
Termoplásticos:
-ABS ( acrilonitrilo-butadieno-estireno): Tiene buenas propiedades en cuanto a rigidez, tenacidad, estabilidad dimensional , resistencia a los productos químicos y buena calidad de las superficies.Se usan en calandras y rejillas, estructuras del salpicadero.
-ALPHA ( abs- policarbonato): Presenta buenas propiedades mecánicas y térmicas es rígido resistente al impacto y con buena estabilidad dimensional. Se utiliza en spoilers, cantoneras, rejillas.
-PA ( poliamida): También conocida como nailon, se fabrica en varias densidades.Es tenaz, resistente al desgaste y a los disolventes usuales.
-PC( policarbonato): Materiales rígidos y duros con una excepcional resistencia al impacto.Son dimensionalmente estables, resistentes a la intemperie y al calor.Es combustible pero de carácter autoextingible. Se utiliza para revestimientos, paragolpes, interiores, pasos de ruedas, carenados de moto.
-PE (polietileno): Es el polímero de mayor producción Es resistente a los productos químicos y a las levadas temperaturas, tiene una gran resistencia a la tracción y al impacto. Se utiliza para baterías, paragolpes, revestimientos.
-PP ( polipropileno): Tiene idénticas aplicaciones que el PE de alta densidad. Es buen aislante y muy resistente a la tracción y a la abrasión.
-PP-EPDM ( etileno-propileno-dieno-monomero): Es elástico y absorbe con facilidad los impactos, es resistente a la temperatura y de buenas propiedades eléctricas. Se utiliza en paragolpes, revestimientos interiores y exteriores.
-PVC (cloruro de polivinilo): Resistente a la intemperie y a la humedad, pero no a la temperatura, por lo que hay que añadirle diversos estabilizantes. Se utiliza en cables eléctricos, pisos de autocares.
Termoestables:
-GU-P ( resinas de poliéster reforzadas con fibra de vidrio): Son materiales rígidos, ligeros y de buenas propiedades mecánicas. Se utiliza en portones, capos, carenados de motos.
-GFK (plásticos reforzados con fibra de vidrio): Presentan una estructura formada por una resina termoendurecible y fibras de vidrio. SE usan en paragolpes, salpicaderos.
-EP ( resina epoxi): Son materiales duros, resistentes a la corrosión y a los agentes químicos no originan encogimiento. Se utiliza como adhesivo para los metales y para la mayoría de las resinas sintéticas.
Elastómeros:
-PU ( poliuretano) y PUR ( poliuretano rígido): Son la base de diversos elastómeros. Resistentes a la abrasión y na notable resistencia al desgarramiento. Se uso en cantoneras, revestimientos interiores, asientos.
Método de reparación: los materiales sintéticos pueden arreglarse de la siguiente manera:
Soldadura: este procedimiento consiste en aplicar calor hasta que los elementos a juntar se encuentren pastosos y en ese momento juntarles. Para reforzar la unión se aplica un material de aportación de la misma composición.

Acetona: con este elemento químico se puede llegar a unir piezas pequeñas. Al aplicar un poco de acetona en la parte que queremos juntar, ésto se pone pastoso y blando por lo cual juntamos las dos partes y lo dejamos secar y obteniendo un resultado bastante bueno.
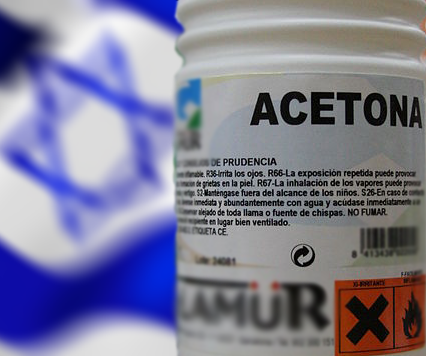
Adhesivos: en la reparación de materiales sintéticos en los vehículos se utiliza generalmente unos adhesivos de poliuretano o resinas epoxi.
4-Hitos históricos que marcan la vida de los materiales sintéticos.
Como hito en los materiales sintéticos hablaré de la invención del plástico. El invento del primer plástico se origina como resultado de un concurso realizado en 1860, cuando el fabricante estadounidense de bolas de billar Phelan and Collarder ofreció una recompensa de 10 000 dólares a quien consiguiera un sustituto del marfil natural, destinado a la fabricación de bolas de billar. Una de las personas que compitieron fue el inventor norteamericano John Wesley Hyatt, quien desarrolló el celuloide disolviendo celulosa (material de origen natural) en una solución de alcanfor y etanol. Si bien Hyatt no ganó el premio, consiguió un producto muy comercial que sería vital para el posterior desarrollo de la industria cinematográfica de finales del siglo XIX.
En 1909, el químico norteamericano de origen belga Leo Hendrik Baekeland sintetizó un polímero de gran interés comercial, a partir de moléculas de fenol y formaldehído. Se bautizó con el nombre de baquelita y fue el primer plástico totalmente sintético de la historia, fue la primera de una serie de resinas sintéticas que revolucionaron la tecnología moderna iniciando la ''era del plástico''. A lo largo del siglo XX el uso del plástico se hizo popular y llegó a sustituir a otros materiales tanto en el ámbito doméstico, como industrial y comercial.
Baquelita
En 1919 se produjo un acontecimiento que marcaría la pauta en el desarrollo de los materiales plásticos. El químico alemán Hermann Staudinger aventuró que éstos se componían en realidad de moléculas gigantes o macromoléculas. Los esfuerzos realizados para probar estas afirmaciones iniciaron numerosas investigaciones científicas que produjeron enormes avances en esta parte de la química.
No olvidemos también el vulcanizado como hito histórico. La vulcanización es un proceso mediante el cual se calienta el caucho crudo en presencia de azufre, con el fin de volverlo más duro y resistente al frío. Fue descubierta por Charles Goodyear en 1839 por accidente, al volcar un recipiente de azufre y caucho encima de una estufa. Esta mezcla se endureció y se volvió impermeable, a la que llamó vulcanización en honor al dios Vulcano. Sin embargo, hay estudios que demuestran que un proceso similar a la vulcanización, pero basado en el uso de materiales orgánicos (savias y otros extractos de plantas) fue utilizado por la cultura olmeca 3.500 años antes para hacer pelotas de hule destinadas al juego de pelota mesoamericano de la época precolombina. Durante la vulcanización, los polímeros lineales paralelos cercanos constituyen puentes de entrecruzamiento entre sí. El resultado final es que las moléculas elásticas de caucho quedan unidas entre sí a una mayor o menor extensión. Esto forma un caucho más estable, duro, mucho más durable, más resistente al ataque químico y sin perder la elasticidad natural. También transforma la superficie pegajosa del material en una superficie suave que no se adhiere al metal o a los sustratos plásticos
Breve historia del vulcanizado:
La historia del caucho es antigua. Los mayas y los indígenas meso-americanos extrajeron el látex orgánico de los árboles de Castilla elástica (caucho o hule) de los bosques americanos. Transformaban esa viscosa sustancia en pelotas, y jugaban con ellas el juego de pelota, con connotaciones sagradas: los perdedores eran a veces, ejecutados ritualmente. Esas pelotas no podían durar mucho más que los jugadores ganadores. El caucho natural no curado se vuelve muy oloroso y en pocos días comienza a pudrirse. El proceso de putrefacción tiene, en parte, relación con la ruptura de las proteínas, como sucede con las proteínas de la leche, pero también a la ruptura de las largas moléculas de caucho a medida que se oxidan en el aire o en tierra.
Goodyear clamó que le correspondía el descubrimiento de la vulcanización basada en azufre en 1839, pero no patentó su invento hasta el 5 de julio de 1843, y no escribió la historia de su descubrimiento hasta 1853 en su libro autobiográfico, Gum-Elastica. Mientras tanto, Thomas Hancock , un científico e ingeniero, patentó el proceso en el Reino Unido el 21 de noviembre de 1843, ocho semanas antes de que Goodyear ejerciera su propia patente en el Reino Unido.
5-Materias primas para la producción de materiales sintéticos.

Los materiales sintéticos son creados a través de materiales naturales que encontramos en la Tierra, algunos de esos materiales naturales son:
Extraídas de los animales:
Piel: a la hora de hacer cuero necesitamos la piel de los animales. Proviene de una capa de tejido que recubre a los animales y que tiene propiedades de resistencia y flexibilidad bastante apropiadas para su posterior manipulación. La capa de piel es separada del cuerpo de los animales, se elimina el pelo o la lana, salvo en los casos en que se quiera conservar esta cobertura pilosa en el resultado final y posteriormente es sometida a un proceso de curtido.
Herramientas para el trabajo del cuero
Lana: la lana es una fibra natural que se obtiene de los caprinae (cabra y, principalmente, ovejas), y de otros animales, mediante un proceso denominado esquila. Se utiliza en la industria textil para confeccionar productos tales como sacos, mantas, guantes, calcetines, suéteres, etc.

Lana
Extraídas de la naturaleza (plantas, árboles..):
Madera: la madera es un material ortótropo, con distinta elasticidad según la dirección de deformación, encontrado como principal contenido del tronco de un árbol. Los árboles se caracterizan por tener troncos que crecen año tras año, formando anillos concéntricos correspondientes al diferente crecimiento de la biomasa según las estaciones, y que están compuestos por fibras de celulosa unidas con lignina. Las plantas que no producen madera son conocidas como herbáceas.
Madera de pino
Corcho: es la corteza del alcornoque y la encina. Un tejido vegetal que en botánica se denomina felema y que recubre el tronco del árbol. El corcho puede presentarse en bruto, como producto directo de la extracción de la corteza del árbol o elaborado para su utilización en diferentes áreas. El principal componente del corcho es la suberina.
Corteza de un alcornoque
Algodón: El algodón es una fibra textil vegetal que crece alrededor de las semillas de la planta del algodón, un arbusto del género Gossypium, perteneciendo a la familia de las malváceas, originario de las regiones tropicales y subtropicales, hay diferentes especies autóctonas en América, África o la India. La palabra algodón deriva del árabe.
Planta de algodón
Extraídas de los minerales:
Mármol: el mármol es una roca metamórfica compacta formada a partir de rocas calizas que, sometidas a elevadas temperaturas y presiones, alcanzan un alto grado de cristalización. El componente básico del mármol es el carbonato cálcico, cuyo contenido supera el 90 %, los demás componentes, considerados “impurezas”, son los que dan gran variedad de colores en los mármoles y definen sus características físicas. Tras un proceso de pulido por abrasión el mármol alcanza alto nivel de brillo natural. El mármol se utiliza principalmente en la construcción, decoración y escultura. A veces es translúcido, de diferentes colores y puede aparecer de coloración uniforme, jaspeado (a salpicaduras), veteado (tramado de líneas) y diversas configuraciones o mezclas entre ellas.

Suelo de mármol
Arena: La arena es un conjunto de partículas de rocas disgregadas. En geología se denomina arena al material compuesto de partículas cuyo tamaño varía entre 0,063 y 2 milímetros (mm). Se utiliza en la industria del vidrio.

Dunas de arena
Carbón: el carbón o carbón mineral es una roca sedimentaria de color negro, muy rica en carbono y con cantidades variables de otros elementos, principalmente hidrógeno, azufre, oxígeno y nitrógeno, utilizada como combustible fósil. La mayor parte del carbón se formó durante el período Carbonífero (hace 359 a 299 millones de años). Es un recurso no renovable.

Hay muchos más materiales extraídos de la naturaleza, he puesto los más así conocidos.
Con esto doy por finalizado la entrada de hoy sobre los materiales sintéticos. Se puede pensar que sin conocerlos digas que no sabes que son o que nunca les has visto, pero después de lo aprendido todo o casi todo lo que ves tiene materiales sintéticos.